Penn State's Wastewater Treatment System: Embracing Water Sustainability
- David M. Swisher
- Mar 8, 2019
- 8 min read
Updated: Dec 16, 2022
The Pennsylvania State University owns and operates a wastewater treatment plant (WWTP) that is located at 501 University Drive in State College Borough, Centre County. Penn State’s WWTP has been in operation since the early 1900’s, and provides sanitary sewer service to a majority of the University Park Campus and a small portion of the State College Borough in the College Heights District. Map 1 shows the current Sewer Service Area for the Penn State WWTP.

Map 1. Sewer Service Area for Penn State WWTP
The WWTP has a hydraulic capacity to treat up to 4.0 million gallons per day (MGD) of wastewater, and a design organic capacity of 9,500 pounds of biochemical oxygen demand (BOD) per day (Photo 1). BOD is a measurement of the quantity of oxygen consumed by microorganisms, and is typically used to determine the strength of municipal wastewater. In 2017, the Penn State WWTP had an annual average flow of 1.46 MGD, and an annual average organic loading of 2,994 pounds BOD per day.

Photo 1. PSU Wastewater Treatment Plant
The Penn State WWTP is comprised of two treatment trains: one to provide treatment of the liquid wastewater, and one to provide treatment of the solids. A process flow diagram of the liquid treatment train at the existing WWTP is shown in Figure 1.
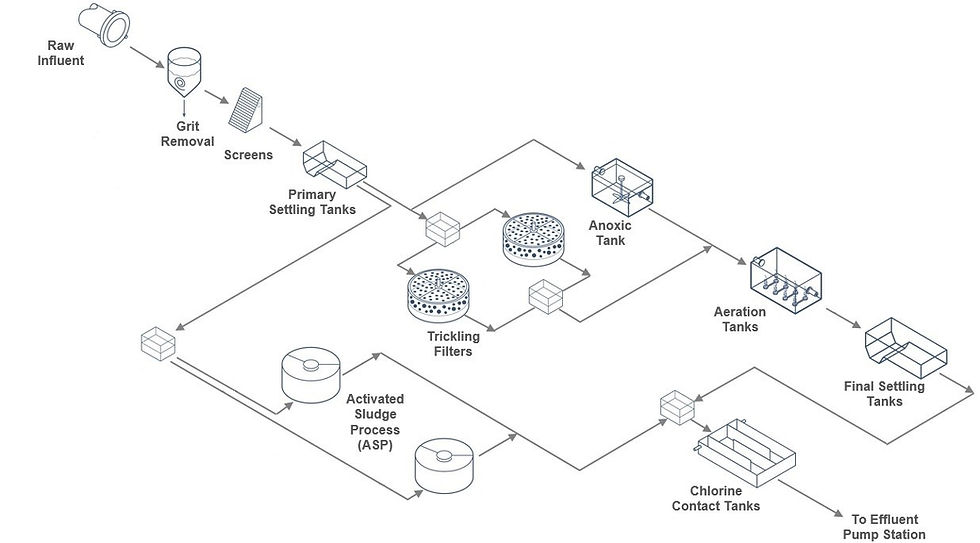
Figure 1. Liquid Train Process Flow Diagram
The liquid treatment train generally consists of the following elements:
Grit Removal and Classification System: The grit removal system provides removal of grit and other inorganic particulates from the raw wastewater. Grit is typically composed of sand, small rocks, and other dense materials that find their way into a sewer system. It is important to remove this grit material from the raw wastewater, as it can accumulate in downstream treatment tanks and cause abrasion in piping and pumps. A grit classifier is utilized to clean and dewater the grit, which is then collected in a container for disposal at the landfill.
Coarse Screening: Two coarse screens are operated in parallel to provide removal of large debris from the influent wastewater. This debris typically includes rags, plastics, wood and other materials that may clog or damage downstream equipment. The debris that is collected by the screens is cleaned, dewatered and collected in a container for disposal at the landfill.
Primary Settling Tanks: Three rectangular primary settling tanks are operated in parallel to remove settleable solids from the wastewater. The large volume in these tanks causes the flow of the wastewater to slow down, which allows solids to settle to the bottom. A chain and flight scrapping mechanism moves the solids to a hopper, where they are removed from the tank and conveyed to the solids treatment train. After the wastewater flows through the primary settling tanks, the liquid is conveyed to one of two biological treatment systems: the Trickling Filter Process Treatment System or the Activated Sludge Process Treatment System.
Trickling Filter Process (TFP) Treatment System: A portion of the liquid from the primary settling tanks is conveyed to an anoxic tank, and then to two activated sludge aeration tanks. This series of tanks provides for the biological removal of organics and nitrogen that is in the wastewater. Liquid is also conveyed to two rock-media trickling filters that are operated in parallel (Photo 2 and 3). In the trickling filters, the wastewater trickles down over the rock media to also provide for the biological removal of organics and nitrogen from the wastewater. Once the wastewater has been biologically treated, it is conveyed to two rectangular final settling tanks. Solids collected in the bottom of the settling tanks are either returned to the process as returned activated sludge (RAS), or wasted to the solids treatment train. The treated liquid, or effluent, from the final settling tanks is then sent to the chlorine contact tanks for disinfection.
This series of tanks provides for the biological removal of organics and nitrogen that is in the wastewater. Liquid is also conveyed to two rock-media trickling filters that are operated in parallel (Photo 2 and 3). In the trickling filters, the wastewater trickles down over the rock media to also provide for the biological removal of organics and nitrogen from the wastewater. Once the wastewater has been biologically treated, it is conveyed to two rectangular final settling tanks. Solids collected in the bottom of the settling tanks are either returned to the process as returned activated sludge (RAS), or wasted to the solids treatment train. The treated liquid, or effluent, from the final settling tanks is then sent to the chlorine contact tanks for disinfection.

Photo 2. Trickling Filter Tanks
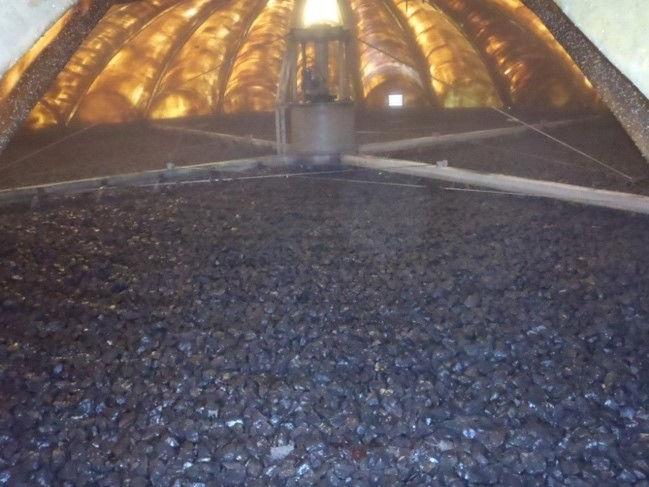
Photo 3. Trickling Filter System Rock Media
Activated Sludge Process (ASP) Treatment System: In the activated sludge treatment system, two circular tanks are utilized (Photo 4). The center of each circular tank serves as an aeration zone for the activated sludge process, while the outer ring of each tank is used for a final settling tank. Aeration and mixing are provided to the liquid in the center ring of each tank, which allows for the biological removal of organics and nitrogen from the wastewater. After biological treatment in the center ring, the wastewater flows to the outer ring where the solids settle to the bottom of the tank. The solids, which primarily consist of the microorganisms that provide biological treatment of the wastewater, are collected at the bottom of the tank and are either returned to the process as RAS, or wasted to the solids treatment train. The effluent from the final settling tanks is then sent to the chlorine contact tanks for disinfection.
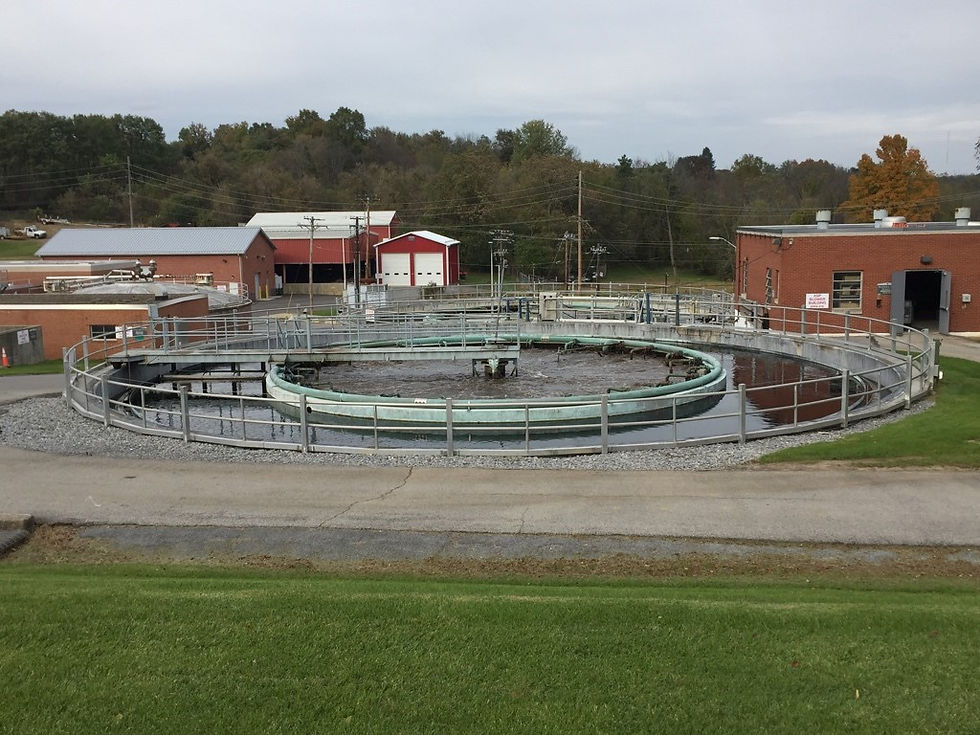
Photo 4. Activated Sludge Process Treatment System
Disinfection: Two chlorine contact tanks are operated in parallel to allow for the disinfection of the effluent. Liquid chlorine is added to the effluent to provide for the removal of potentially harmful microorganisms that may still be present in the water. Following disinfection, the treated effluent is conveyed to the effluent pumping system.
From the time the wastewater enters the Penn State WWTP, it typically takes between 12 and 18 hours to flow through the liquid treatment train. As outlined above, the liquid treatment train utilizes physical, chemical and biological processes to effectively and efficiently remove pollutants from the wastewater. The WWTP typically removes over 99% of BOD and 98% of suspended solids from the wastewater.
The solids produced at the Penn State WWTP are treated with an anaerobic digestion system. A process flow diagram of the solids processing train at the existing WWTP is shown in Figure 2.

Figure 2. Solids Train Process Flow Diagram
The solids treatment train of the existing WWTP generally consists of the following elements:
Dissolved Air Flotation Thickener: The dissolved air flotation (DAF) thickener provides thickening of the solids from the final settling tanks. The thickened solids are then conveyed to the primary anaerobic digesters, while the liquid that is removed from the solids is conveyed back to the beginning of the liquid treatment train.
Primary Anaerobic Digestion: Two primary anaerobic digesters receive and treat solids from the primary settling tanks and the DAF thickener. The anaerobic digestion process uses microorganisms to break down biodegradable solids in the absence of oxygen. Solids remain in the digesters for approximately 20 days. Digested solids from the primary anaerobic digesters are then conveyed to the secondary digester. The anaerobic digestion process naturally produces biogas, which is composed primarily of methane and carbon dioxide. Penn State collects this biogas and utilizes it to heat the contents of the digesters and to provide heat to several buildings onsite.
Secondary Anaerobic Digestion: One secondary anaerobic digester is utilized to provide additional treatment of the solids and to provide storage of the digested solids prior to dewatering. Treated solids from the secondary anaerobic digester are periodically conveyed to the dewatering system.
Dewatering System: One rotary press is utilized to dewater the digested solids. The purpose of the dewatering process is to remove water from the solids. The solids are pumped from the secondary digester to the rotary press system, where they are mixed with polymer to enhance the removal of water. The conditioned solids are then conveyed through the rotary press system to squeeze out the water. The dewatered solids, known as biosolids, are collected in a dumpster for disposal at a landfill. The liquid removed from the solids is conveyed back to the beginning of the liquid treatment train.
Living Filter
In Pennsylvania, the majority of wastewater treatment plants discharge the treated effluent directly to a surface water source such as a stream or river. However, the Penn State wastewater system is unique, in that there is zero discharge to a stream. Since 1983, Penn State has been recycling all of its treated effluent through a land application system known as the Living Filter (Photo 5). The Living Filter consists of approximately 600 acres of agricultural land and forest land (Photo 6 and 7). An estimated 90% of the irrigated water recharges the region’s water table—about 1.3 MGD, or over 475 million gallons per year. The land application of treated effluent provides enhanced treatment of the water as it slowly percolates through the soil profile, helps to maintain base flows in streams such as Spring Creek, and reduces the impacts of drought conditions. The Penn State WWTP has not discharged to a stream since 1983, and is thought to be one of the many reasons that the water quality of Spring Creek is considered to be better now than any time in the last 100 years. Management of the Living Filter system is provided by the Wastewater Management Committee, a multi-discipline committee made up of researchers from across the University, as well as representatives from the Pennsylvania Department of Environmental Protection and the Pennsylvania Game Commission. Research completed by this Committee is transmitted via trade journals and research publications to advance the knowledge base on wastewater treatment plant processes and land application systems.

Photo 5. Living Filter Signage
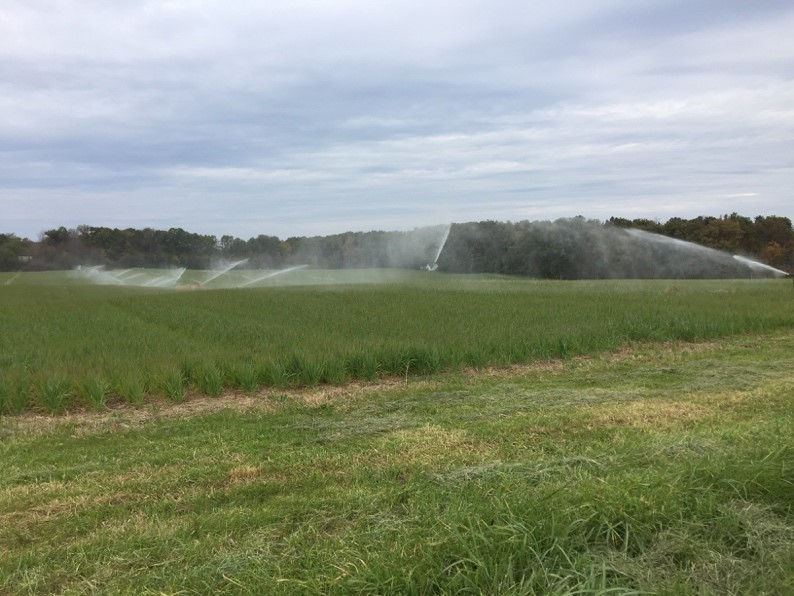

Photos 6 and 7. Land application of treated waste water
Using Reclaimed Water
To further promote the sustainable use of water, the University has developed a master plan for the future implementation of a reclaimed water system for the University Park Campus. This reclaimed water system would take a portion of the treated effluent from the WWTP and make it available for appropriate water uses on campus. It is estimated that strategically using reclaimed water on campus could reduce groundwater withdrawals by 300,000 to 500,000 gallons per day. Sewage facilities planning and permitting has been completed for the system, and installation of portions of the reclaimed water distribution system has begun as opportunities present themselves. Targeted uses for the future reclaimed water system include toilet flushing, irrigation, vehicle washing, non-potable washdown and laundry. When viable, interior plumbing systems of new or renovated buildings on campus are being installed in a manner to facilitate the use of reclaimed water when it becomes available.
The University is currently undergoing the design and construction of a major capital upgrade to the existing WWTP. Sewage facilities planning for these upgrades was approved in March 2018 by the Centre Region Council of Governments through an Act 537 Plan Special Study. Upgrades to the WWTP are needed to renovate and replace aged infrastructure, improve onsite safety and improve the treatment and energy efficiency of the facility. Based on future wastewater flow projections for the University Park Campus, a 3.0 MGD design capacity is recommended for the upgraded WWTP. The upgrades will generally include a complete rebuild of the liquid treatment train utilizing membrane bioreactor technology, and will include improvements to screening, grit removal, flow equalization, disinfection, solids thickening, odor control, and electrical/controls systems. The upgrades to the Penn State WWTP are expected to be complete by 2022.
About the Author: David M. Swisher is a licensed Professional Engineer with over 15 years of environmental engineering experience in the water and wastewater industry. He serves as the Wastewater Utility Engineer for the Penn State Office of Physical Plant, and is responsible for providing engineering support to the wastewater systems at all of Penn State’s campuses.
Comments